THE V8 MAN CAVE
PART 1
Family, the dog and health aside, my garage is the most important part of my life. It is a haven where I can escape the stresses and strains of everyday life. It is where I go to lock myself away from the real world and fashion my automotive creations. I have built seven cars to date, beginning with my Ferrari Dino replica at the tender age of 17, followed by three evermore powerful Westfields, a NOS-injected fake snake, a 350 bhp V8 powered Dax Rush, and, of course, my ultimate creation, the 200 mph plus Ultima GTR. Elsewhere on this site you will find imagery from the V8 years, my last 4 builds which were propelled by the finest cylinder configuration know to man.

All my builds have one thing in common: all were constructed in the same garage. Yes, spanning some 33 years, the same four concrete walls and - leaky - corrugated iron roof (recently upgraded to tiles) has seen a procession of cars built from the chassis up. In the early days the ageing building was my father’s country garage business, during which time I populated a dark corner with a tiny bench and one electric socket. However, the day came when he retired and I became the proud owner of Bridge Garage. It was duly closed as a business and became my bolthole, inspection pit and all.
​
THE EARLY YEARS
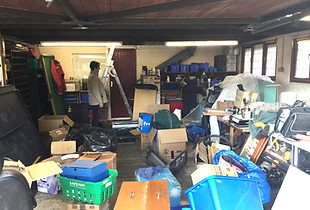
I did my best to spruce the place up on my father’s retirement: removal of prison doors he had utilised as work benches for over 40 years (just don’t ask me how he got his hands on those) and requesting a local builder to extract a three tonne tank turret (which, according to Dad, made an extremely reliable tube bender for fabricating racing go-kart frames) being a couple of the more memorable moments. With limited funds, I applied a lick of emulsion to the grease-laden walls and glued some second-hand carpet tiles to the floor, and that, as they say, was that for the next 20 years or so with pauses between builds seeing my beloved space become a dumping ground.
THE INSPIRATION
However, my life was about to change when I stumbled across the phenomenon of fitted garages thanks to an invitation to the Aston Martin One 77 production facility. On entering the glistening white workshops my eyes were not drawn to the line of handcrafted million-pound beasts, but instead - you guessed it – to the gloss white garage units. It was an apparition. The wall of exquisitely crafted doors and drawers resembled something from an F1 garage or futuristic operating theatre. In an awe-struck, quivering voice I whispered, ‘Oh my God, just look at your garage’, and headed at haste towards the 50 feet long stretch of tool cabinets, my guide following behind in complete bemusement. Yes, the cars were a beauty to behold, but the garage! It took a good 20 minutes to pull me away from those units. It was akin to clapping eyes on my firstborn for the very first time. Enough was enough, my life would not be complete without my own ultimate man cave, so project V8 Man Cave commenced.

CREATING THE CANVAS
Like an artist requiring a canvas my garage needed perfectly flat insulated walls and ceiling – just like those in a brand new house. Even though I consider myself pretty handy the thought of plastering an entire room measuring 20 feet by 30 feet did not sound easy. After surfing the Internet for a while I decided to drywall the whole area. This requires a wooden studwork frame along all walls with vertical battens at 600 millimetre centres. The gaps are then filled with insulation pads and the lot covered with plasterboard sheets. Special plasterboard with chamfered edges is used to hide the butt joints. Once in situ, a length of wet tape is stuck along the join (in the recess) and plaster applied with a wide 8 inch blade. Once dry, two further applications of plaster are required. Finally, the plaster is sanded and, once decorated - in theory - you cannot see the joins.
Watching YouTube made this whole process look simple. The truth of the matter is the wooden frame was indeed very straightforward, almost enjoyable, in fact, despite an engine not being involved. Nice and clean, no wet stuff and plenty of time to stand back with a beer and admire progress. Providing you take your time and get everything true, it all comes together pretty quickly. The real ballache, however, was the fixing of those large, fragile sheets of plasterboard, especially on the ceiling. Making the joins (and screw holes) disappear required some effort and was rather messy. Finally, the sanding part (using 120 grit paper and sanding pole) created so much dust I had to escape for air on a regular basis notwithstanding the use of a face mask throughout. By now you may be getting the impression I didn’t like this part of the build, and you would be spot on. However, patience, patience, Peroni, patience, and another Peroni eventually saw the job completed. It just seemed to go on forever.
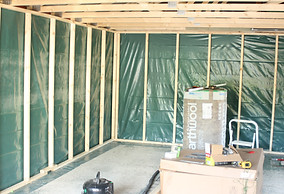


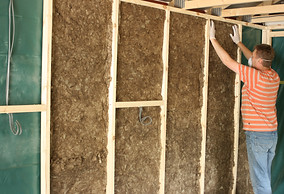





BEER TIME
I agree it has all been a bit Bob the Builder this month. Next month, however, comes my favourite part, the clean work prettifying the space: fitting the LED lighting, laying the flooring and installing those oh-so-amazing wall and floor cabinets. Until next time, happy spannering.
